By Stephen Brown and Kasey Snell
Grain bins can range in size depending on the facility's needs and are used to store commodities or other products for later use. Products that you might find in a grain bin include grain or other granular material.
In 2020, 64 fatal and non-fatal incidents related to agricultural confined spaces were reported and 32 of these incidents involved a fatality. How can we, as an industry, reduce this number? Utilizing best practices and easily installed products can significantly reduce the number of times a farmer or farm worker should need to enter a grain bin and decrease many of the unsafe factors related to working around grain and grain storage structures.
Proper moisture during harvest time is a crucial factor when storing commodities inside a grain bin. When harvesting commodities at high moisture levels, the facility must have a plan in place to stop spoilage. It is important to properly dry a commodity when placing grain inside a grain bin. If moisture is imbalanced, it can cause hot spots, clumping, or bridging to occur. Make sure that all grain being placed inside the grain bin is suitable for the projected storage time. Prior to storing grain or any product in a grain bin, inspect the bin to make sure that it has been properly maintained. Before filling a grain bin, check the bin’s roof and vents to ensure they are properly sealed to reduce the risk of weather and moisture negatively affecting your commodity from spoilage. A final check is to visually look for cracks or missing bolts on your grain bin panels or foundation. If cracks or missing bolts are present, make repairs before using the bin. Repairs and maintenance left unchecked can lead to an increased chance of spoilage and decreased structural integrity of the bin.
Grain Bin Fall Protection Systems
According to the Bureau of Labor Statistics, there were 35 fatalities and 4,870 non-fatal injuries due to falls, slips, and trips in the agricultural industry. Fall arrest systems can be installed on grain bins as the tie off point for the person climbing the ladder. A typical setup includes a set length of rope or cable that is the correct size for the bins at your operation. Paired with the rope or cable will be two steel snap hooks that should be connected to the bottom and top of the bin. An example of this setup can be seen in Figure 1. The rope or cable would be positioned directly beside the ladder and extend multiple feet above the top entry door of the bin. This setup allows the person to remain attached to a safety line when entering a bin door. From the top of the bin roof, you can unhook and reposition your harness to the safety line inside of the bin. In 2018, the American Society of Agricultural and Biological Engineering (ASABE) S624 recommended anchor points be placed inside of a bin. The bin manufacturer should be consulted to determine if anchor points can be installed in all pre- and post- 2018 bins. For a fall protection system, each employee should have their own harness fitting their body type and weight.
New grain bins being constructed may have the option of adding stairs to replace the ladder for safer access to the bin roof and hatch. As shown in Figure 2, spiral staircases are both safer and ergonomically easier to climb than the standard grain bin ladder. As mentioned previously, anchor points within a grain bin are optional and not standard when building a grain bin. If installed by a grain bin manufacturer, anchor points would be placed at the peak of the roof and a foot below your top entry. The anchor point below the top entry door is mounted to the top panel of the grain bin. Anchor points are a very important option when entering through the top hatch on a grain bin. Anchor points and lifeline harness systems help eliminate the possibility of an engulfment or entrapment within a grain bin.
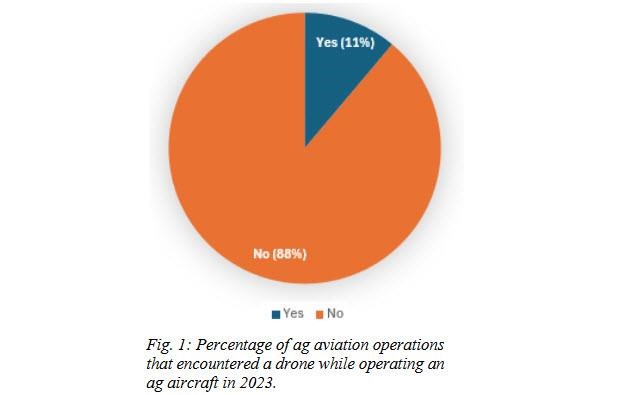
Figure 1. Rope grab and harness connection for fall protection system.
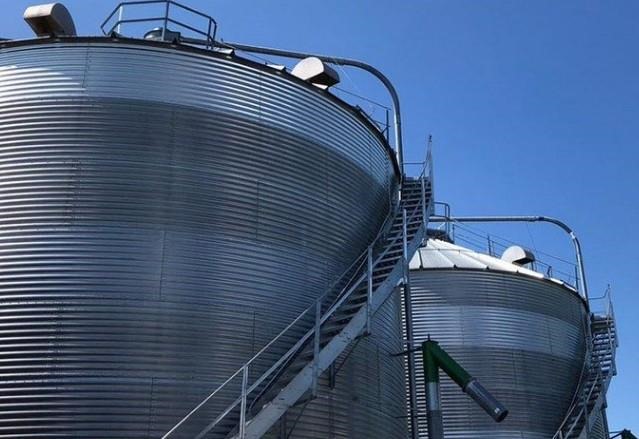
Figure 2. Grain bin with spiral staircase.
Grain Level Indicators
Grain level indicators allow employees to view the grain levels while remaining on the ground. This simple device includes a flap on the bin’s interior wall and an indicator device on the bin’s exterior wall to easily view the levels of the grain inside the bin. As shown in Figure 3, the grain level indicator uses the pressure of the grain pushing against the flap on the interior wall which changes the exterior wall device a distinct color to easily show the level inside the bin. Grain level indicators should be installed in a vertical line with adequate spacing between each indicator. The amount of grain level indicators depends on the size of your grain bin. This system helps mitigate spillage as well as proper filling height of a grain bin.
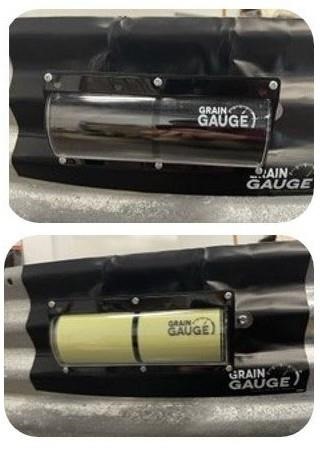
Figure 3. Grain level indicator activated vs. not activated.
Lock out/Tag Out
Grain entrapments and engulfments can occur from a variety of situations including the collapse of a grain bridge, avalanche of a grain wall, and by flowing grain or using a grain vacuum. One way to reduce the risk of grain entrapment is to practice proper lockout/tag out procedures for securing energy sources. As shown in figure 4, all energy sources have been shut down and completely secured before entry occurs. Every employee should be notified of the lock out/tag out before entry occurs which alleviates the possibility of sumps or side draws being opened for use. As shown in Figure 5, a lock out/tag out kit includes multiple locks for each employee and a card that should be completed prior to attaching to the power supply. Each lock is given one key with no replication so the employee who locks out the power supplies is the only person able to remove their lock. Lock out/tag out kits can be purchased from various local and online retailers who specialize in industrial or agricultural safety. Kits are available with multiple fixtures that cover a broad range of breakers and plugs to secure equipment. When a situation occurs, where multiple employees must be involved, each employee should place their own lock on the suggested lock out device prior to entry.
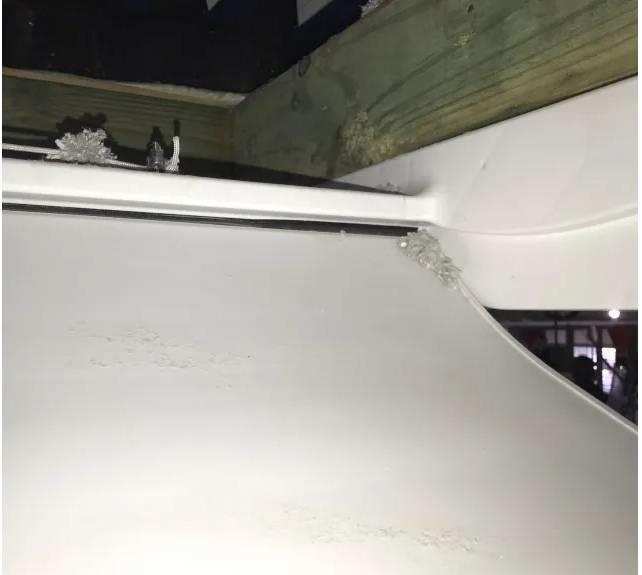
Figure 4 (left). Lockout/tag out on safety switch. Figure 5.(right) Components of lockout/tag out kit.
Clump Busting Equipment and Sump Guard
Grain clumping occurs when a moisture imbalance is present inside of a grain bin and can reduce or stop the flow of grain causing a potentially hazardous situation. Entrapments and engulfment can occur when employees enter the bin and try to break up clumped grain from inside. To avoid this, commercial products are available that have shown effectiveness in assisting the flow of grain. Power sources for these products may vary such as a common cordless drill or a hydraulic motor attached to a tractor which can be seen in figure 6. Regarding designs, some products are placed directly over the sump of the grain bin while others are attached to a permanent sweep within the bin that disconnects when the sweep is running.
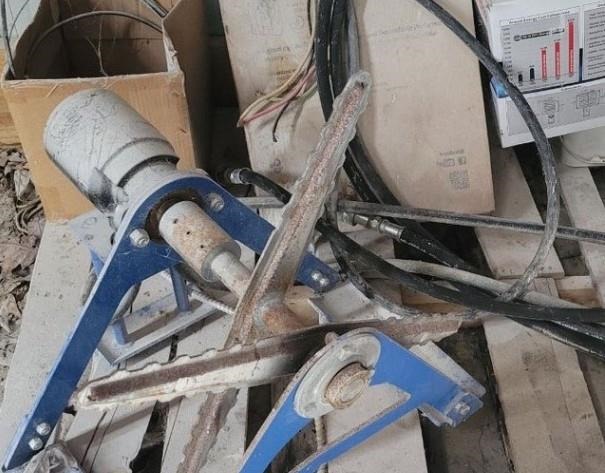
Figure 6. Sump guard that connects to tractor's hydraulics.
Conclusion
By reducing the number of grain bin entries and working with the bin manufacturer to install anchor points on a grain bin, the number of injuries and fatalities can be decreased. The first step is following best practices when harvesting and storing your commodity at the recommended moisture level. Out of condition grain is one of the main factors in entrapment and engulfment incidents. Commercially available products such as bin level indicators to monitor grain levels and clump busting equipment to promote proper grain flow can decrease the need to enter the bin. If a person does need to enter a grain bin, the person should be equipped with the properly fitted harness and lifeline system that is attached to a manufacturer-installed anchor point. Prior to installing an anchor point to a grain bin, the farm owner or manager should consult the grain bin manufacturer to have them determine if their grain bin can safely accommodate an anchor point and lifeline system. Fall protection systems and spiral staircases on grain bins both improve access and reduce the risk of slips, trips, and falls. Utilize lock out/tag out to properly shutdown and secure power supplies. Make safety a top priority at your agricultural operation.
Source : psu.edu