By Rainey Rosemond
As feed costs continue to rise and impact the bottom line, feed efficiency is becoming increasingly important to producers. While the formulated ration is critical to keeping feed costs within reason, on-farm feed management should be a focus to ensure that formulated rations are effectively delivered to all cows.
Critically important in total mixed ration (TMR) feeding systems is the consistency of the ration delivered to cows. Rations varying in weights of each ingredient, total weight delivered, particle size distribution, mixing order, or mixing time could impact individual cow performance.
Total weight delivered and the weight of each ingredient included in rations is impacted by the feedstuffs' dry matter (DM). If feed DM changes from the previous week or with weather events, this could impact the actual amount of feed being added to the mixer. Shifts in the amount of each ingredient added can alter the nutrients making it to the bunk. It is a best practice to check feed DM weekly to ensure adequate and consistent amounts of each ingredient are incorporated into rations.
Figure 1. Depicts varying particle size in feed.
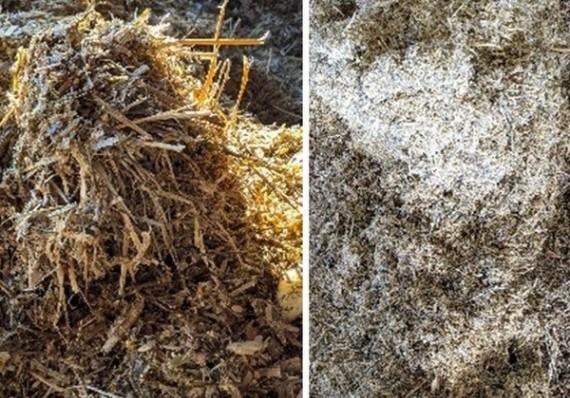
Particle size distribution within rations is also important to cow health and performance. A TMR lacking adequate particle size could negatively affect health and result in production issues associated with inadequate fiber. Herds with low physically effective fiber could experience milk fat depression. Additionally, low physically effective fiber can lead to metabolic problems if saliva production drops as additional chewing is no longer stimulated. On the other hand, having long chopped forages or forages that do not mix well could lead to sorting. This would appear as though ration nutrients are being adequately delivered to the bunk, but issues with cow health and performance could result from rations too low in physically effective fiber.
Mixing time also plays a part in particle size distribution. If rations are mixed for too long, forages could become too fine. Similarly, if rations are not mixed long enough, hay or long-chopped forages could come out in clumps and be easily sorted. Mixing time will vary from farm to farm based on the mixer's recommendation. Manufacturer’s instructions should be followed and after all ingredients are added to the mixing wagon, allow for standing mixing time on a flat, even surface before delivering feed to the bunk. To avoid varying post mixing time from day to day keep a timer present at the time of mixing.
Daily monitoring of refusal amounts can offer insights into forage or feed moisture changes as well as group dynamics. High-producing dairy cows should have from 1-3% refusals, while low producing or dry cows can be fed to 0.5-3% refusal levels. Properly adjusting the percent refusals up or down requires daily monitoring. To ensure milk production is not negatively impacted, adjust management strategies when the targeted refusal amount is not met. Refusals amounts lower than the desired percentage may indicate the cow requires more energy, and the delivery amounts should be increased. Similarly, when refusals are high, energy intake may decrease, and initial delivery amounts can be reduced. Further investigation is warranted when drastic swings in the amount of feed remaining at the bunk are detected. Collecting daily refusal weights and using this information to calculate estimated feed intake per cow allows producers to more effectively monitor feed efficiency.
Source : psu.edu