By Dennis Brothers
Growers should consider and investigate many factors in the broiler industry before purchasing a commercial poultry farm—type of farm, revenues and expenses, condition of the houses, required capital, insurance, startup costs, farm loans, and even lifestyle. Learn more in this third of a five-part series for new farmers in the commercial broiler industry.
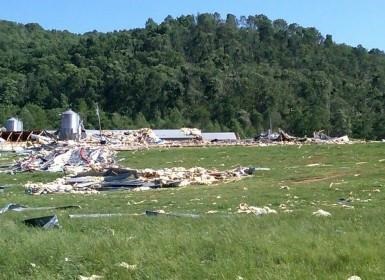
Estimating Revenue & Cost Over Time
When considering the purchase of an existing farm, one of the top priorities is establishing a reasonable estimate of revenue and operating costs. The farm’s past IRS Schedule F form is typically used for this evaluation. Historically, many lenders have based their decisions on a 3-year Schedule F evaluation of a farm. This may be sufficient for a pullet or breeder farm but can cause problems when evaluating a broiler farm.
Broiler farms are paid at the end of a flock, and the flock lengths and downtimes between flocks can vary; therefore, a farm may not receive the same number of flocks every year. If you calculate an average number of flocks per year, you may get a partial flock as part of the year’s revenue. Since the farm is paid only at the end of a completed flock, this partial payment is not actually realized that year.
Example:
A farm averages 4.5 flocks per year. In the first year, they receive four flock payments; in the next year, they receive five; and in the third year, they receive four payments. Averaging these 3 years on a revenue basis underestimates the 3-year average at 4.3 flocks of revenue per year. If the 3-year evaluation starts with a five-flock year, then four, then five again, the average is overestimated at 4.7 flocks per year. It is therefore recommended that at least 4 years be analyzed to get a more accurate annual revenue estimate; more years is usually better to avoid assuming a skewed average.
Careful evaluation of bonus payments becomes important to revenue estimates similarly. Some bonus payments correspond to the flock cycle, and annual revenue may be affected when flocks take place during the year. For example, if three flocks take place during a wintertime fuel bonus pay period in one year and only two flocks qualify for the bonus the following year, the annual gross revenue will vary greatly.
Knowing this information is especially important when evaluating farms receiving new housing bonuses. Not all new housing bonus payments appear on a normal flock settlement report; therefore, tax return information may not correspond with flock reports. Buyers also need to know if they qualify for the new house bonus as a new owner, how many years are left on the bonus contract, and how that contract will be paid out.
Before buying, request to see as many actual flock settlement documents as possible and compare how the farm performed in relation to competing farms. A farm that has historically performed below average in weight per bird, feed conversion, or egg production should be closely scrutinized for facility deficiencies that may directly contribute to poor performance. These deficiencies can often be addressed, but must first be identified.
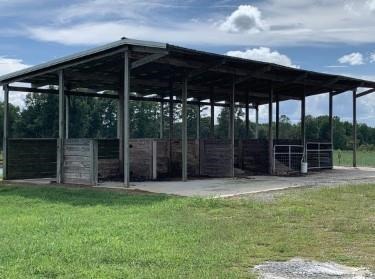
Consider cost evaluation as well, as the flock cycle similarly affects cost. Utility cost tends to follow weather patterns and the corresponding ages of flocks. For example, if a farm has experienced extremely cold weather that corresponded with multiple young-aged flocks for 2 out of 3 years, those 3 years of utility costs could be inflated due to heating fuel expense compared to a 5-year average. A couple of years of extremely hot weather on older birds can similarly skew cost figures due to increased electricity expenses. The opposite effects can also skew costs to the low side for brief periods.
The bottom line is that the longer you can look back and analyze past revenue and cost for a farm, the more accurate a future cash-flow estimate becomes.
Utility Costs
A good measure to consider when evaluating an existing farm is the utility costs of electricity and heating fuel to gross revenue ratio (U/GR). This involves simply dividing the annual utility costs by the annual gross revenue to get a ratio indicative of the farm’s structural integrity and overall energy efficiency (insulation, tightness, equipment energy efficiencies.) A good target for this ratio is 0.25 or less. Newer, more energy-efficient farms may fall below 0.20. Farms with U/GR ratios above 0.30 should be scrutinized closely for inefficiencies.
Animal Facility Considerations
Age & Physical Condition of Structures & Equipment
A prospective buyer should have someone well versed in the structural and equipment aspects of poultry facilities closely inspect a farm. Areas of concentration include insulation throughout, structural integrity and airtightness, equipment condition, and energy efficiency. The integrator’s technical field staff can be a valuable contact in this area. They may have the expertise or have contact with a local expert. Specifically, expert inspections of the structural, electrical, heating, and ventilation systems are top priorities.
The integrator will have minimum specifications for placing their birds on a specific farm. Entering into a sales agreement is not recommended unless a written confirmation is obtained from the integrator ensuring a farm’s current acceptability or outlining specifically what needs to be done to meet their minimum criteria, including what can be done to qualify for any premium pay rates not currently met.
A proper facility inspection informs the buyer of the life expectancy of the structure and equipment before repairs or replacements are expected. Before a contract is granted, an integrator often requires that some equipment be upgraded or replaced due to age or poor condition. These requirements should be agreed upon and in writing before a purchase agreement is made. Sometimes rectifying these situations can be negotiated with the seller as part of the sales contract; if not, the cost to repair or replace should be considered when negotiating a final price and negotiating the loan.
Water Quality
The availability of quality water on the farm is a consideration that is often overlooked. Broiler and breeder farms use vast amounts of water. Water quality is essential both for the birds and for the longevity of drinking and cooling systems. Supplying it can have a significant impact on operating costs and performance.
Some farms have municipal water sources where quality is seldom a concern, but quantity and cost are problematic. Many farms are located on the periphery of municipal systems and can suffer from line volume and pressure losses when the farm needs the most water. Existing municipal and farm plumbing deficiencies also can cause quantity restrictions.
Water can be problematic in well sources. Many farms have wells where both quality and quantity must be monitored. Growers may consider well water free, but treating or filtering well water that is less than desirable quality can be quite expensive. Well water mineral impurities, such as iron, manganese, and calcium, can cause serious problems with poultry house equipment. Excessively high or low water pH is also a concern in many well systems, negatively affecting bird performance or equipment longevity.
If the past performance of a farm is less than desirable, water quality and availability should be closely examined. If purchasing a farm on primarily well water, a water sample should be evaluated by a testing lab or the results of a current test should be reviewed before purchasing.
Water problems can sometimes be addressed by having additional water sources. Many integrators are requiring farms to have two water sources. This may be required of an old farm before a new owner can secure a contract. This could mean adding a well to a municipal- supplied farm or vice-versa. In some cases, additional wells are allowed to meet the multiple source requirement.
Serious water issues like any of the above can be costly to address and must be factored into a farm purchase decision.
Generator System
The backup power generator system is a specific area of concern often overlooked during a farm inspection. These systems are critical for the operation of the farm and require specialized knowledge to accurately ascertain their condition and readiness to operate as needed. A professional generator service inspection should be completed on the system or evidence of a recently completed (within 1 year or less) professional service be provided before purchase of a farm.
Additional Capital Considerations
Every poultry operation requires rolling equipment to operate. Tractors, trailers, litter-handling equipment, and the like, must all be accounted for in the farm purchase. If this type of equipment is part of the purchase, have it inspected, and have any maintenance requirements accounted for as part of the business loan. If additional rolling equipment is required, consider those capital needs as well.
Have any existing outbuildings inspected and consider any future outbuilding needs. Litter sheds are especially valuable assets on a broiler farm. If a litter shed does not currently exist, it is recommended that one be added to the business plan.
Mortality disposal is the sole responsibility of the contract grower; therefore, mortality management systems must be inspected. Have composting sheds, mortality freezers, or incinerator facilities and equipment checked for condition and proper operation.
Insurance and Start-up Costs
Insurance coverage is critical for any poultry farming operation and is required before a lender finalizes a loan. Insurance coverage for commercial poultry farms is becoming difficult to secure in some areas, and the cost can be prohibitive. It is advisable to contact potential insurance carriers early in the purchasing process.
Insurance companies often inspect the facility and may require that structural or equipment maintenance be performed before binding coverage. Additional types of coverages should be discussed, such as loss of income or business interruption coverages, equipment mechanical failure coverages, and whether the farm facilities qualify for replacement cost value or depreciated cash value coverage for property damages.
Of these coverages, loss of income or business interruption coverage must be carefully evaluated. Most policies will replace all or most income lost directly to a covered peril. For instance, if fire destroys a house, a typical poultry farm insurance policy with loss of income coverage would replace a significant portion of the income that would have come from the lost flock of birds. However, policy limits may prevent payment for all the income lost during the reconstruction phase. It is recommended that a policy have loss of income coverage limits that equal or exceed 6 months of normal net revenue to allow for farm repair while not imposing financial hardship.
Start-up Costs
Every farm purchase has additional start-up costs. These can include recurring flock inputs, such as litter, chick feed trays, diesel fuel for the generator and rolling equipment, litter ammonia treatments, litter beetle pesticide, and sanitation products. Other costs to be considered include utility deposits and hookup fees, monthly utility bills due before flock payment, and weekly labor expenses. For larger farms, more than 10 percent of gross revenue could go to hired labor.
The capital to cover expenses must be at hand to start the business. Too often, new growers are unprepared for these expenses and quickly find themselves deep in credit card debt or encumbered with other high-interest short-term loans. Having substantial working cash on hand is always the best option. However, adding a percentage of these expenses into the farm loan upfront can be a viable option that will cost less than using unsecured debt as a capital source.
The amount of working capital needed varies with farm type and size. Location and season also can impact immediate working capital needs in the form of heating fuel or electricity requirements. If these bills come due before a flock settlement takes place, then working capital must be at hand to cover them.
A lender should be able to give a purchaser guidance on how much working capital is needed for a comparable farm in the area. Broiler farms typically see the most significant impact from a lack of working capital due to the delayed nature of the revenue stream. For example, a farm producing a 60-day flock could see 2 months of utility bills and labor costs due before any revenue can offset those costs.
For broiler farms in general, one quarter (25 percent) of a farm’s annual variable expenses should be available for working capital. With pullet and breeder farms, which are paid biweekly or weekly, working capital needs are lower but still must be considered. Once a farm is up and running and revenue is coming in, proper budgeting should include establishing a working capital amount sufficient to carry the farm through for several months.
Farm Loan Payment Considerations
One somewhat unique aspect of commercial poultry production is the payment of the farm loan. Under almost all situations, the lending institution has an assignment agreement with the grower and the integrator. Per this agreement, the integrator sends a portion of the contract pay directly to the lender to cover the annual loan payment. This guarantee of payment arrangement has been integral in making contract poultry one of the more attractive agricultural businesses to finance.
The exact payment calculations vary with lending institutions and farm types. In general, 45 to 50 percent of the gross revenue of a farm is used to pay the farm loan. Suppose the purchase price is on the higher side, however, and the buyer has less than a 20 percent equity position. In that case, the resulting loan payment can be above 50 percent of gross revenue and become a barrier to cash flow.
The payment schedule for a pullet farm is usually calculated as the total annual loan payment divided by the number of weeks in a year the farm has birds. For breeders, it can be more complicated. Most breeder assignments are based on a percentage of production; therefore, the payment amount will not be consistent week to week. On the positive side, this allows a grower to retain a fairly consistent operating margin through productivity gains and losses. However, if there is a low- producing flock overall, a balance of the annual payment due could remain at the end of the year.
For broilers, a variety of payment methods exist. Sometimes the annual payment is divided by the number of whole flocks per year. Other times a set percentage of the flock payment is paid. This method could lead to some balance of the annual payment remaining at the end of the year. The method by which bonus payments, such as utility bonuses or new housing bonuses, are calculated into loan payments should specifically be discussed with the lender.
Lifestyle Considerations
Commercial poultry operation requires significant labor and daily management, although the specific requirements may vary with farm type and size. Before investing:
- Talk to as many other growers as possible to get a good idea what daily life will be like on the farm type you are considering.
- Consider future quality-of-life expectations and costs.
- Decide if poultry farming requirements and income will result in your desired lifestyle. Long-term success requires a certain amount of financial discipline. Living outside of what the farm provides is often a cause of poultry farm business failure.
Most integrators require contract growers to live on the farm property or within a defined distance from the farm. If living accommodations exist on the farm, their suitability should be factored into the purchasing decision, along with any needed repairs or upgrades desired. If not, the cost of accommodations should be calculated into the overall business plan.
A good understanding of a poultry farm’s potential ups and downs is important before entering this business. A contract poultry farm is considered to have an overall low risk from market changes compared to many other farming businesses, but it does not come with zero risk. Understanding what risks exist can help growers make better business decisions. And, as with any business, lower risk often comes with lower potential returns
on investment. For more information, see the first article in this series, ANR-2932, “Farm Types and Estimated Business Returns” on the Alabama Extension website www.aces.edu.
Business Entity Choice and Financing
A commercial poultry farm is a large agribusiness entity. Careful consideration is needed as to the kind of business entity chosen, as it has direct impacts on income taxes, business liability issues, and future farm succession questions. The business structure chosen, whether a limited liability company, a sole proprietorship, or other, can have significant impact on how the business fits into the household income-tax structure.
One of the first steps to take in moving forward on a new farm purchase is to contact a competent accountant and attorney skilled in a new business setup. It is beneficial if they have experience with agricultural businesses.
Additional Resources
- “NPTC Tools of the Trade: Measuring Water Flow Rate” on the Alabama Extension website at www. aces.edu
- “Nutrient Management Planning for AFOs” on the Alabama Extension website at www.aces.edu
- “Mortality Disposal Methods for Commercial Poultry Growers: on the Alabama Extension website at www. aces.edu
- “New Farmers Guide to the Commercial Broiler Industry: Business and Financing” on the Alabama Extension website at www.aces.edu
Definition of Terms
- AFO/CAFO. USDA Natural Resource Conservation Service designations for animal feeding operations and confined animal feeding operations. Any farm housing more than 100,000 birds at a time is considered a CAFO and required to meet stricter NRCS guidelines.
- Assignment agreement or loan assignment. Agreement between integrator, lending institution, and grower that allows the integrator to make direct payment for the farm loan to the lending institution out of the grower’s contract pay before the grower receives the pay.
- Breeder farm. Grower-owned housing for producing hatching eggs to be hatched for broilers.
- Broiler. Chicken grown to a specified weight for meat production.
- Broiler farm. Grower-owned housing for broiler grow out.
- Bonus pay. Any payment that is not part of the normal contract base pay rates. These can be limited to a specific period, time of year, housing category, or other parameter. Can be based per pound or per square foot (SF). Examples are new house bonus pay or cold weather fuel bonus.
- Feed Conversion. A ratio representing the number of pounds of feed needed to produce one pound of live bird at market weight.
- Hen (breeder hen). Mature female chicken producing hatching eggs.
- Integrator. Major poultry-producing company (e.g., Tyson Foods, Pilgrim’s Pride, Koch Foods). These companies own the birds, supply the feed, and are responsible for all aspects of transporting, processing, and marketing the birds.
- Pullet. Sexually immature female chicken.
- Pullet farm. Grower-owned housing for raising breeder hens and roosters from chicks to sexual maturity.
Source : aces.edu