By Ryan Bergman
Claims of poor fertilizer application and visual striping in fields have increased in recent years. This issue impacts all sectors of the supply chain including growers, custom applicators, cooperatives and agribusiness insurance companies. An increase in documented application problems is primarily driven by a broader use of aerial imagery that can easily detect problems and an increase in use of dry nitrogen fertilizers. Cases of poor-quality application are seen less frequently with phosphorus or potassium products than with nitrogen because corn is not as sensitive to varying rates of these nutrients. Prior to applying dry fertilizer, follow these guidelines to achieve the best possible quality during application.
Calibrating the spreader
Whether using a spinner spreader or an air boom-type spreader, the machine should be properly calibrated. Machines should be calibrated every year for each product and should be re-calibrated if product conditions change throughout the season. It’s important to calibrate the product metering system as well as checking the distribution across the spread width of the machine. Complete spread pattern test kits are available to support this. This online article (FABE-561) from The Ohio State University explains this calibration process.
Calibrating the product metering system involves collecting and weighing product as it comes off the conveyor. This ensures the control systems spins the conveyer at the proper speed based on the machine ground speed, gate opening, and product density.
Checking spread distribution involves setting catch pans on the ground and driving the machine over them while applying (Figure 2). Each pan is dumped into an individual vial and measured to examine the spread distribution across the width of the machine (Figure 3).
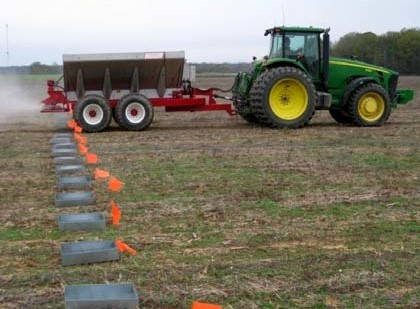
Figure 2. Typical distribution of fertilizer calibration pans that are spread across the width of the spreader to catch calibration samples. The fertilizer spreader is operated at typical field application speed and rates to determine the distribution of material across the width of a spinner spreader. (Image courtesy of The Ohio State University FABE-561)
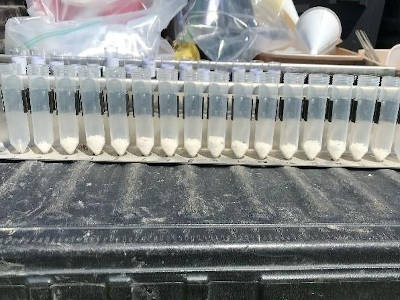
Figure 3. The small amount of product on each end of the pattern is expected since this is from a dual spinner machine, which relies on some pass-to-pass overlap to ensure a full rate is applied at the edges of the spread width. Notice the vial in the center appears to have more product than the surrounding vials. Overapplying in the center of the machine is a common issue with poorly adjusted spinner and air boom type machines. Information on correcting spread pattern problems can be found in this article (FABE-562) from The Ohio State University.
Spinner spreader distribution patterns often shift based on product density and application rate. It is typical to see distribution patterns that create a “W” pattern behind the spreader when application rates increase (Figure 4). Maintaining a consistent pattern across the width of the machine under all application rates is critical to eliminate local nutrient deficiencies. This is particularly important when applying nitrogen fertilizer due to increased crop responsiveness to reduced application rates.
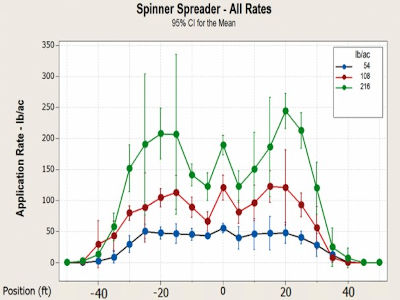
Figure 4. Example application pattern from a spinner spreader under three different application rates when spreading dry Urea. The application pattern shifts towards a W pattern as the application rate increases.
Many spreaders can do a high-quality job of applying fertilizer; however, the fertilizer applicator is responsible for making the appropriate adjustments to optimize the machine for a specific product and rate.
Understanding the machine’s application distribution allows the applicator to adjust the machine as environmental conditions change. For instance, as wind speed and direction changes, it is crucial to evaluate how this affects distribution and to make needed adjustments. This may include changing the driving direction or adjusting spinner speed to narrow the application width to mitigate any negative impacts.
Monitor product quality
One of the biggest causes of change in spreader distribution throughout the year is variability in product quality. It’s important to monitor density and hardness of the fertilizer granules as these can change due to storage conditions and environmental effects. Changes to density or hardness can have a direct impact on how fast the spinners can rotate without damaging the fertilizer granules, which affects how far the product can be spread.
To better visualize the effect product density has on spread distance and distribution, picture a golf ball and a ping pong ball. Both are similar in overall size, but the golf ball is heavier than the ping pong ball. The golf ball will travel farther because of the weight difference when thrown.
Product size is measured using a size grade number (SGN) scale (Figure 5) and hardness with a crush strength tester. Both tools are available through an equipment dealer or supporting vendor. These tools should be used to evaluate the product calibrated and to determine if the product quality changes during the season. If the product quality does change, the spreader should be recalibrated.

Source : iastate.edu